TDB-2000L super large extrusion molding machine production line
Suzhou Tongda Machinery Co., Ltd. mainly develops, designs and produces a full range of extrusion plastic blow molding machines from 10ml to 2000L. Each year, about 45% of blow molding equipment is sold overseas. In 2009, the company successfully developed China’s largest ultra-large extrusion forming unit – TDB-2000L blow molding tray dedicated unit, mainly used for the full range of blow molding trays and high-speed production of ultra-large hollow blow molding products. The successful development of TDB-2000L marks that the research and development level of China’s ultra-large hollow blow molding units has leapt to a new level. The 1616 blow molding tray manufactured by TDB-2000L is the widest blow molding tray in the width direction at home and abroad. The single weight of the product is about 55kg. It is the single heavyweight product in China. This product has been mass-produced and applied to a large enterprise. In 2011, the company successfully developed the TDB-1200L blow molding tray production line. The equipment was sold to Xinjiang PetroChina Pipe Company, which is mainly used to produce blow molding trays of various specifications within 1614.
In the first half of 2010, the company successfully developed the first “Ming Ze Ling” flexible curved ring radial dynamic die control system and static mandrel control system, which can effectively realize multi-directional control of plastic parison. These two control systems are the original technology of Chinese engineering and technical personnel, and have won a number of national invention patents and utility model patents. The flexible loop of the control system has a diameter range of 150~850mm, which can adapt to the requirements of different product models and different blow molding products for different die diameters. At the same time, it can realize multi-point adjustment of flexible loops of the die to 2~16 points. control. The mandrel flexible loop control system has up to 18 to 36 control points and control accuracy of up to 0.1 mm. The successful development of these two high-tech products represents that the comprehensive innovation capability of China’s extrusion plastic blow molding machine has reached the international advanced level, and it has also created favorable conditions for the development of various shaped blow molding products. The flexible curved ring control system is expected to enter the installed test and batch manufacturing in 2012. In addition, Suzhou Tongda also carried out research on hydraulic system servo motor and variable pump system, which has obvious energy-saving effect. Compared with conventional hydraulic system, single item energy saving is more than 30%.
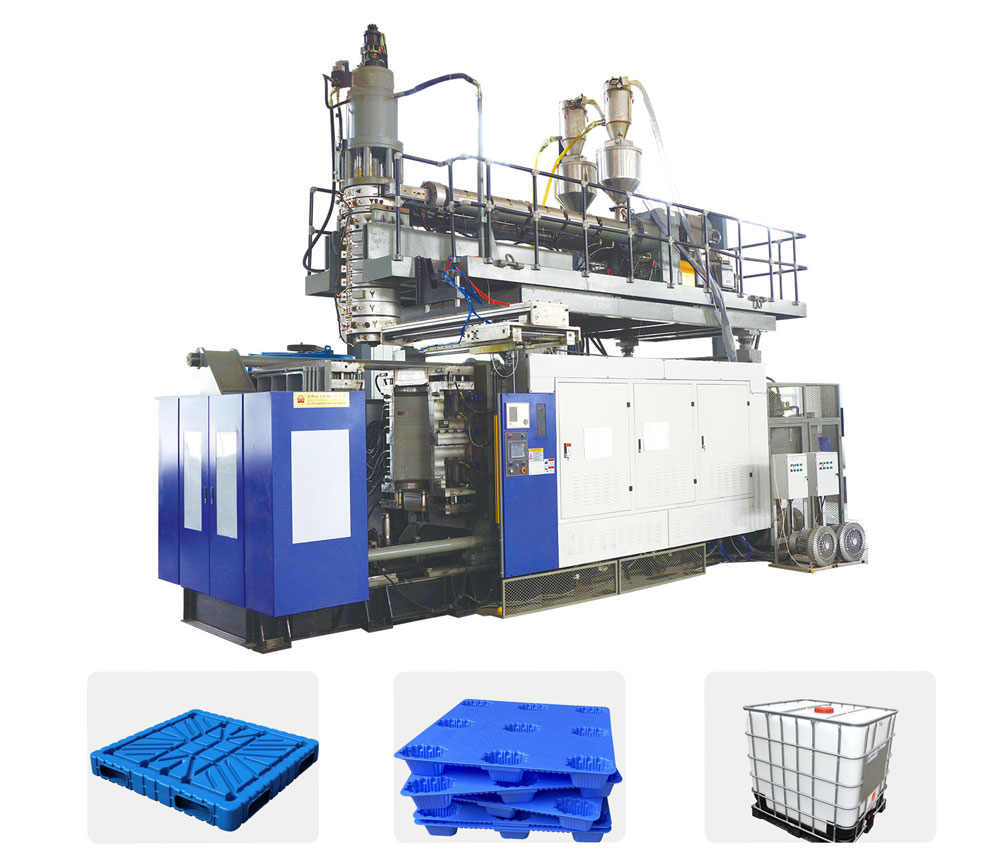