Requirements and implementation of extrusion blow molding process
The premise of the extrusion blow molding process requires that the compression atmosphere of the parison in the inflated mold must be clean. The injection blow molding atmosphere pressure is 0.55 ~ 1MPa; the extrusion blow pressure is 0.2l ~ 0.62MPa, and the stretch blow pressure is often as high as 4MPa. In the plastic coagulation, the high pressure causes the internal stress of the finished product to be low, the stress evacuation is relatively average, and the low stress can improve the tensile, striking, tortuous functions and the like of the finished product. 1.2 The finished product has two types of blow molding products: container and industrial parts.
The container therein includes: a packaging container, a large volume storage tank/storage tank, and a collapsible container. However, with the maturity of the blow molding process, there are more and more blow molded products for industrial parts, and the scale of utilization is becoming more and more common. At present, containers account for about 80% of the market share, an increase of 4% per year; while industrial and layout finished products account for 20% of the total, with an annual growth rate of 12%. The increase in container consumption is due to the continuous expansion of the use of twistable and twisted plastic containers. The increase in the consumption of industrial finished products is mainly due to the improvement of new processing techniques, such as multi-layer parison extrusion, biaxial extrusion, and non- Axisymmetric blow molding, etc.
Blow molding pause
(1) During the molding process, the raw material polymer is affected by high shear force when passing through the die, and then the material exhibits signs of extrusion shrinkage and shrinkage, and the shrinkage rate of the parison when forming the drooping parison
Close to zero. The parison is then inflated against the mold, at which point a low shrinkage occurs. Moderate die shrinkage can result in waste. Moderate sag causes the thickness of the top to bottom wall thickness of the part to be uneven, severe or even impossible to form. Therefore, when selecting a properly blown polymer, it is necessary to clarify the viscoelastic characteristics of shearing and shrinking.
Due to its good thermal stability and a variety of modified products, HDPE is the most commonly used plastic in blow molding. Through the copolymerization and blending effects, the research on the raw materials for blow molding has also suffered some pauses in the continuous extrusion of blow molding grade resins, such as PA6, PP and PET. Intermittent parison blow molding is theoretically applicable to secondary processing of layout sheets and large parts, requesting application of engineering plastics such as flame retardant abs, reinforced PVC, modified PPO and PC, etc. The high temperature resistance of plastics is as common as usual, and most of the resins can be blow molded into large parts on conventional equipment.
In the blow molding of polyethylene naphthalate (PEN)/PET blends, it is necessary to prevent oxygen from seeping into the exudation and leakage of water into the exuded resin such as (ethylene/vinyl acetate) copolymer (EVOH) and HDPE and PET form a composite layer and an anchor layer occurs to improve the infiltration and thermal stability of the PEN/PET material. At present, we are considering the adoption of multi-layer blow molding of HDPE and PA6, and the fuel tank of the basin.
(2) Equipment and process skills pause
Blow molding machinery and equipment have been greatly improved. The newer results are: 1 adopting improved infrared heating technology to stop re-blowing; 2 abnormal high-speed torsional extrusion pressure, which is mainly used in the milk bottle; 3 mold attached to the shuttle press to compensate for the jet Signs; 4 multi-layer continuous extrusion blow molding to prevent seepage into the exudation container; 5 through the process of orientational crystallization and thermal crystallization, preform and mold temperature, blowing pressure, and parison pause time in the cavity Strict control, stop the production of continuous heat-set PET bottles.
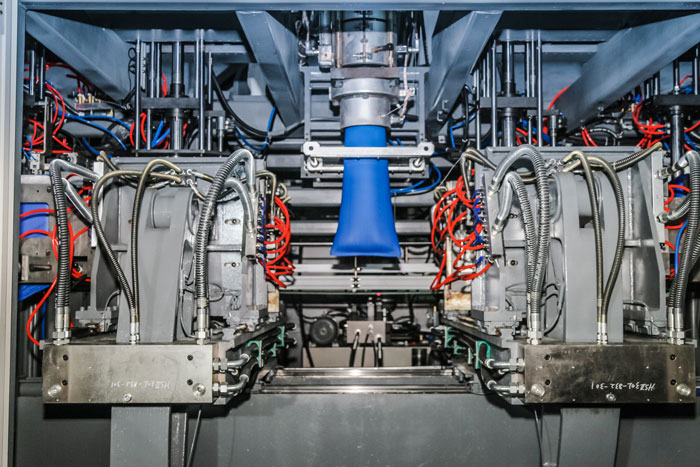
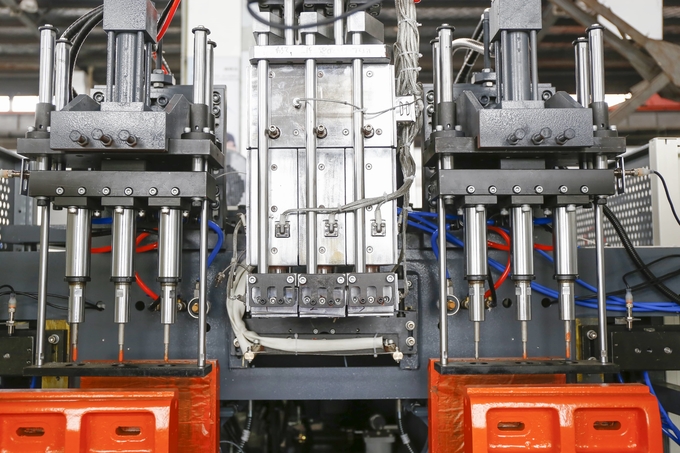